Steel Marking Advancements: Elevating Manufacturing Processes for Superior Outcomes
In the realm of making procedures, steel stamping has long been a foundation method for generating a range of accuracy components. With the ruthless march of technological advancement, the landscape of metal stamping is going through a considerable improvement.
Development of Steel Stamping Strategies
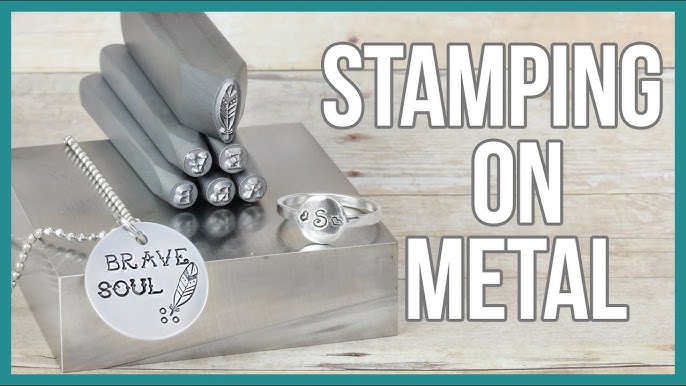
Furthermore, advancements in product science have resulted in the growth of high-strength alloys that can currently be perfectly marked right into complex shapes, accommodating a more comprehensive series of industrial applications. The integration of robotics and expert system has further maximized the marking procedure by enhancing rate and accuracy while decreasing the risk of human mistake.

Impact of Advanced Materials
Have sophisticated products transformed steel stamping procedures substantially in the manufacturing market? By utilizing products such as high-strength alloys, advanced compounds, and innovative layers, metal marking processes can currently produce parts that are lighter, stronger, and extra resilient than ever before.
These sophisticated materials supply premium mechanical properties, rust resistance, and thermal stability, permitting makers to meet the needs of modern-day sectors such as aerospace, automobile, and electronic devices. Furthermore, the usage of advanced materials in steel marking has actually facilitated the manufacturing of complex geometries and detailed styles that were formerly unattainable via conventional techniques.
In addition, the implementation of sophisticated products has actually led to reduced material waste, reduced manufacturing prices, and much shorter preparations, making steel stamping processes more affordable and sustainable. As technology continues to advance, the impact of sophisticated materials on metal stamping procedures is anticipated to drive more technology and boost the competition of producers in the worldwide market.
Automation in Metal Stamping
The evolution of metal stamping procedures driven by the assimilation of sophisticated materials has actually established the stage for significant advancements in automation within the production market. Automation in metal marking has transformed production procedures, improving efficiency, accuracy, and general output top quality. With the usage of robotics, sensors, and computer-controlled systems, tasks that were once manual and time-consuming can currently be executed with unequaled rate and accuracy.
Automation in metal stamping not just increases manufacturing prices however likewise makes sure consistency in the manufacturing procedure. By minimizing human intervention, the threat of errors is significantly lowered, bring about greater degrees of product harmony and dependability. Additionally, automation makes it possible for makers to undertake intricate stamping jobs that would be challenging or not practical to accomplish manually.
Moreover, automation in steel stamping adds to a much safer working setting by reducing the demand for employees to take part in recurring or harmful jobs - Metal Stamping. This change towards automation not just boosts efficiency yet also paves the method for the future of production, where modern Recommended Site technology plays a central duty in driving functional excellence
Top Quality Control and Assessment Equipments
With a focus on precision and dependability, top quality control and inspection systems play a vital duty in guaranteeing product excellence in metal marking processes. These systems are made to keep an eye on every phase of manufacturing, from material assessment to the last item, to guarantee that all elements satisfy the needed requirements. By executing advanced modern technologies such as optical inspection systems, coordinate gauging devices (CMM), and automated determining equipment, makers can identify even the smallest inconsistencies in dimensions, surface top quality, and overall stability of stamped components.
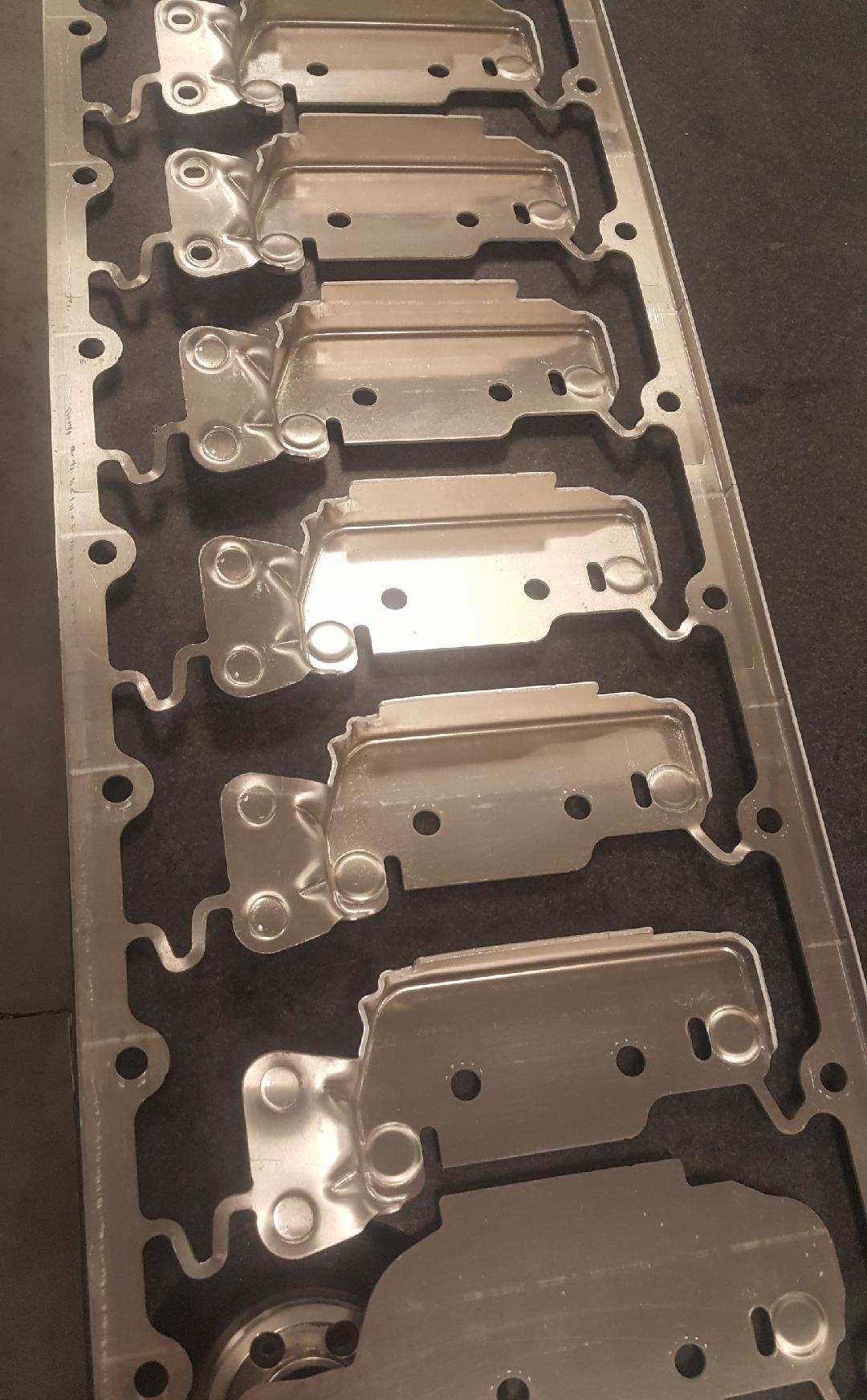
Sustainability Practices in Steel Stamping
Structure upon the structure of precision and integrity established through quality assurance and assessment systems, the integration of lasting practices in metal stamping procedures is progressively coming to be a prime focus for producers looking for to lessen ecological effect and enhance source application. Sustainability techniques in steel marking include a variety of campaigns intended at lowering waste generation, power usage, and greenhouse gas discharges throughout the production process.
One key element of sustainability in metal marking is the fostering of green materials and technologies that advertise recyclability and waste reduction. By utilizing recycled materials and applying energy-efficient machinery, producers can lower their carbon impact and contribute to an extra sustainable manufacturing cycle. Furthermore, enhancing production procedures to decrease product waste and energy usage not just benefits the setting but also brings about cost financial savings for companies in the lengthy run.
Moreover, the application of sustainable techniques in steel stamping can boost brand online reputation and appeal to Going Here ecologically mindful consumers. As sustainability proceeds to get value in the production market, integrating green efforts into metal marking procedures is crucial for long-lasting success linked here and competition on the market.
Final Thought
Finally, metal stamping techniques have substantially evolved gradually, integrating innovative materials and automation to improve producing processes. Quality assurance and assessment systems play a crucial duty in ensuring superior outcomes, while sustainability techniques are increasingly being implemented to lower ecological influence. These advancements in metal marking have reinvented the sector, leading to more lasting and reliable manufacturing methods for different markets.
Metal stamping, once a handbook and labor-intensive procedure, has actually changed right into a very automated and innovative technique of shaping metal sheets into different kinds and layouts.Have sophisticated products transformed metal marking processes dramatically in the production sector? By making use of products such as high-strength alloys, progressed compounds, and ingenious finishings, metal marking procedures can now generate components that are lighter, more powerful, and much more sturdy than ever previously.
The advancement of metal marking procedures driven by the assimilation of innovative materials has set the stage for significant improvements in automation within the manufacturing market.In verdict, metal marking methods have actually substantially progressed over time, integrating advanced materials and automation to enhance producing procedures.